Exciting technological innovations have allowed manufacturers, health care professionals, and farmers to increase their productivity and capabilities. Computer numerical control or CNC is the concept of using computers to control machine tools. It is a manufacturing process that uses computerized machines and cutting tools to remove material from a stock piece, making it a subtractive process. This allows the user to produce a custom part.
The numerical control programs tell the machine how fast to turn their spindle, how fast to move their cutters, what direction to move in, and when to turn off the machine. CNC is commonly used for plastic, wood, glass materials. These machines are capable of autonomously performing the operations which results in the creation of custom parts.
Steps in the CNC Machining Process
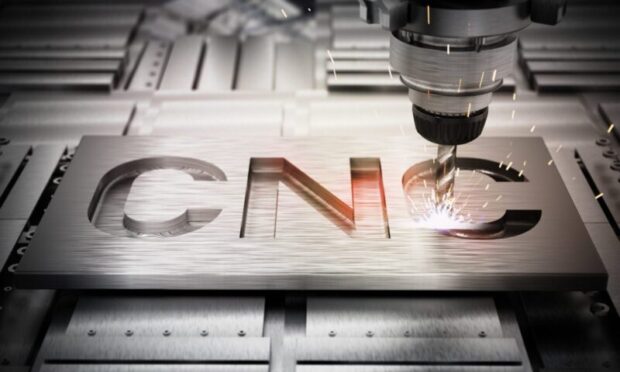
Four steps in the this process lead to the production of custom parts and designs: designing the CAD model, changing the CAD file to a computer numerical control program, prepping the CNC machine, and carrying out the machining operation.
In the first step, a computer-aided design software company (CAD) will create a model of their parts including all the technical specifications. They must take into account the existing machine tooling that is available to them. Some may be limited in their ability to create the necessary design.
The shape of the machine and tooling, conditions of the material being stripped, and minimum part size and thickness can create limitations. The CAD files are then converted to a CNC file which will be handed off to the manufacturer if a CAD company is used for the design.
In the second step, the CAD design file is passed through a CAM software program which will then create code that will instruct the CNC machine on how to use the tools to create the parts. The two most common codes are G-code and M-code. G-code will tell the tools how to move including the pace of work, movements, and positioning. M-code gives information on secondary functions such as taking off and replacing the machine covers when necessary. Once the code is created, the manufacturer can transfer the program to the CNC machine.
In the third step, the machine is prepared for operation by putting the workpiece into the machine through spindles or into vises. The necessary tools such as drills and end mills are then fastened to the corresponding machine components. The manufacturer can now start the program.
In the final step, the machining code is executed, and the tools operate on the desired components. The machine’s integrated computer receives the program’s instructions and uses it to control the movements of the tools.
CNC Applications
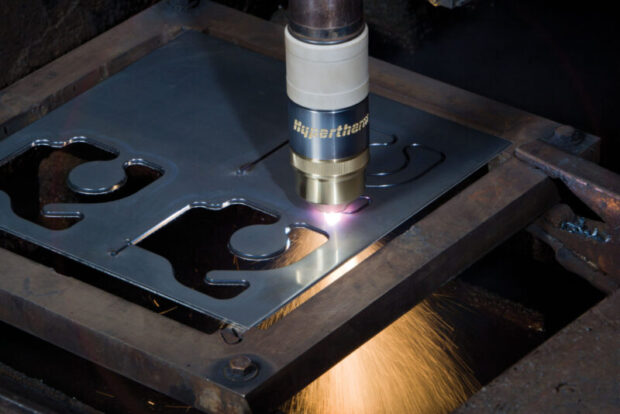
The most common operations employed in the CNC machining are milling, turning, and drilling. There machines can be used to mill the piece to strip it to meet manufacturing requirements. Milling can be performed on flat surfaces with a shallow depth and it can be used to cut deep cavities including slots onto the part. CNC machines can cut on three dimensions, an important advantage over manual machining.
This machinery can also be used for turning, removing material at single points to make tapers, threads, and slots. The CNC machines can also feed rotating drill bits to make holes on the piece. The drill bits can be fed perpendicularly to the piece or they can be fed to accommodate special technical specifications.
This machinery is used in a range of industries, including cars, aircraft, construction, and farming. They are used to create car frames, surgical tools, aircraft engines, and farming tools. CNC machining combines mechanical, chemical, electrical, and thermal processes to produce these goods.
They can bend wire, embroider products, create pottery, and decorate foods such as cakes. Among the most common products produced with machinery are wooden chairs, metal plaques, auto parts, and aviation parts, and metal pieces for smartphones.
CNC machinery is already a popular method of machining and has replaced manual machining. Whereas, machines used to be very large investments available to mainly large corporations, advances in technology have made them more efficient and affordable. Some manufacturers have even built these machines, although they are widely available.
Many have started their businesses using CNC machining for specialty manufacturing with high accuracy. Before starting a CNC machine business, it is important to know the target clients and how much of an investment to make.
The startup costs associated with CNC machining vary, and it depends on what you’re trying to accomplish. Smaller machines can fit in a garage or small workshop, for example, and used CNC machinery from a company like Revelation Machinery is also a great option to reduce startup costs. As the business grows, the range of machining services provided can be expanded using profits to pay for new machinery.
The advantages of using these machines are that the process is accurate, precise, and can increase cost-effectiveness when production is brought up to scale. It is important to note that as the degree of complexity increases the benefits of using CNC decrease. While CNC is great for producing custom parts, as the product designs become more complex, the process’s efficiency and cost-effectiveness decrease.
CNC machines with precise cutting and manipulation abilities are versatile and can operate on almost any part made of wood, metal, aluminum, or alloys. Businesses can use CNC to increase their productivity and free up manpower to focus on other areas of production such as design and marketing.
With the right planning and target market, businesses focusing on providing machining can be successful. Additionally, traditional businesses switching to CNC machinery will see significant increases in productivity.