Factories are huge and a lot of people are working there. That means, there are so many sectors, departments, and workers who are located in different places in the building, and the monitoring process can be pretty difficult. In most industries, people aren’t allowed to use their phones while around the production line. So, as you suppose, communication is crucial, for all things to go smoothly, and for everyone to keep track of what’s happening and how to react when something goes wrong.
In these industries, especially while around the manufacturing production line, the people use their hands for the work, and they can’t really take a call from their boss or other coworkers, since they are very busy. That’s why they use walkie talkie app or even traditional devices, so they can always be on the line with other people, but still managing to do their job as needed.
In factories, production is the main priority, and that’s why they miss the importance of communication, and some misunderstandings happen. If you pay more attention to this aspect of your business and improve the communication with the people on the production floor, your factory will work better, and you will manage all the critical things faster than you can imagine.
If you are looking for good ways to improve the communications in the factory, you need to find the right approach on how to do that and start practicing it as soon as possible. There are many models and strategies, and we will help you with a few of them. Probably you will get an even better idea of how to do that, by following these tips:
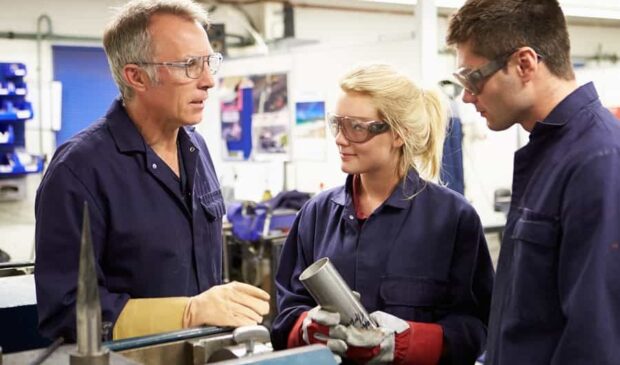
1. Real-time communication is crucial
Not all the employees should be connected to each other, but surely there can be a few of them, who hold important roles in the production process, and should communicate with the supervisors, managers, or even procurement departments. Since face-to-face communication is very limited, using a local phone line, mobile app, or walkie talkie traditional device, with a wide range of coverage, it can become much easier to maintain healthy communication among the crucial people in the production line.
It will help you with voice communication, and sometimes group messages, streams, and notifications are a good way to announce something or demand some change. Mobile technologies are great for real-time communication, and you need to find a proper app that will handle that volume of calls and messages.
2. Evaluate the current situation and see how you can improve it
Before you incorporate something new, you must understand how things are going, and identify the critical points. Where does the communication fail? What you can do to improve it? What are the issues your employees have because of the lack of communication? How the new methods will affect the current workflow?
You have to answer all these questions and analyze the situation, so you can come up with good decisions, that won’t make the work process slower than now. Improving this part of your business is crucial, and all of the people who work on the production line will know how to deal with specific situations, as instructed.
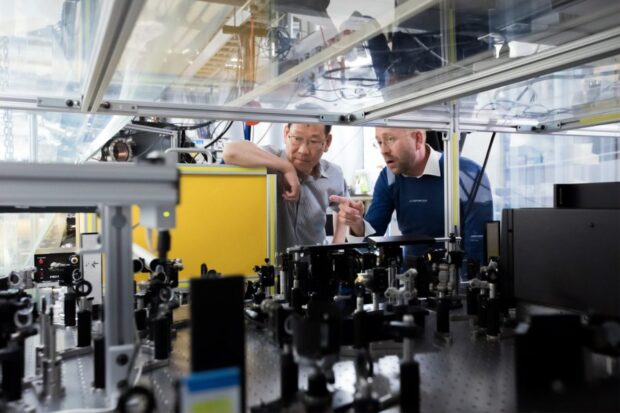
3. Organize regular training
Workers on the line are focused on their tasks, and rarely think about what’s happening in the offices, but you can change that for them. Let them join some training that will improve their communication. It will help them understand the factory’s goal and improve their skills while working. That will result in trust and better turnover because they won’t feel like they are just closed on the floor. Show them they are an important part of the company, and appreciate their efforts, by organizing training for better communication among them.
Also, you can get a better insight into what’s happening on the production floor if you have people of trust. Let them realize how important are they, and the factory will work much better than ever before.
4. Let the workers communicate without you
This is one of the best things to do for the employees. Keep in mind that they are professionals who know their job, and probably they can come up with great solutions without you managing their actions. It’s a great way to help them trust each other, even though it may result in some tiny issues that can be easily resolved. Let them know that they are important and meaningful for the factory and that you trust them completely. This can help you build a good working discipline and environment, and enhance the overall performance of the company.
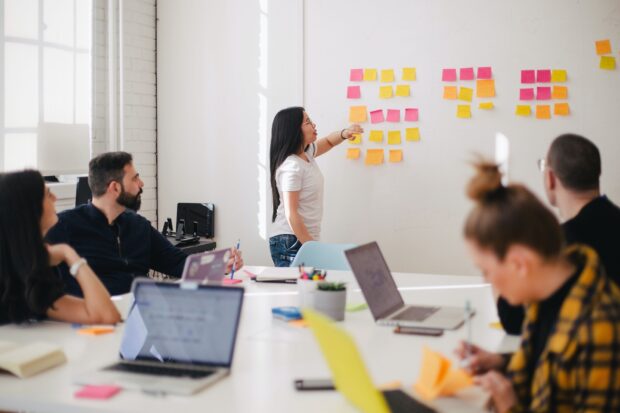
5. Tell them you expect their feedback
Your workers must get back to you with feedback. Don’t let them talk to the other people badly, but listen to them when they are trying to tell you what’s happening in the line. Internal communication is crucial for maintaining a good work discipline, and one of the ways to make sure all things go nicely. But, don’t act like you are deaf when it comes to their issues. No one wants one-way communication. You can’t expect trust and feedback if you act like you are above them all, even though the company’s systematization tells you are. In the end, we are all human, and we are created to communicate with each other, so we can tell what do we want, but also listen to other people and their needs.
Conclusion
Internal communication in the factories is not only using gadgets and devices based on technology. Yes, we can all have that, and that’s their purpose. But, on the other hand, the workers are all people with needs and knowledge that should be heard. Once you establish a strong base for internal communication in the factories, you can expect an even better workflow. That will help you build a strong company, and never be afraid of the competition.
So, learn the basics, get used to them, and do everything you can to incorporate internal communication strategies in the factory.